Paperwork might be the downfall of humanity. Before you can even break ground on a renovation project, you must go through the proper governmental channels. New projects will almost always require a building permit. Foregoing the annoying, but necessary trip to your town’s building permit office can lead to even bigger headaches. Even constructing a simple deck or spare bedroom without the green light from the permit office might leave you picking up a sledgehammer to demolish the simplest of projects. The same is true for constructing a panelized safe room for your home, office or business. While researching the best safe room model for your home, special considerations must be given to your foundation and structural integrity of your home. Our knowledgeable building advisors can guide you through the safe room building permit process.
Measure Twice, Cut Once

New construction and renovation is a finite science. There’s no wiggle room for miscalculations, so you need to consider all variables when determining how to install a safe room. Before pulling the trigger on a new safe room, pick up the phone and contact your local building and plannings office to see if a safe room building permit is necessary for your next project. Previously, government agencies handed down some pretty archaic building codes for safe rooms. This is because safe room construction was a massive undertaking. First-generation safe rooms and bomb shelters didn’t allow for any customization – it was a one-size fits all model that couldn’t be incorporated into any existing floorplan. Old school tornado bunkers just needed a hole in the ground. But times have changed. Changes in building technology and materials have streamlined installation without disturbing existing foundations and interior walls.
In the old days, safe room installation within your home couldn’t be an afterthought. In-house shelters had to be included in the initial build unless you were satisfied with a standalone structure outside the home. But today’s steel manufacturing isn’t your granddaddy’s red iron I-beam days. U.S. Safe Room’s light-weight steel panel technology allows customers to easily retrofit existing rooms and closets into a fortified safe room. We live in dangerous times, so there’s no room for bureaucratic meddling when it comes to protecting your family. Most building permits processes can take up to six months before you can ever break ground on an add-on or structural overhaul. You need turnkey protection without delay. Feeling the pressure of overstressed populaces, many towns have begun relaxing the steps to secure a safe room building permit.
How a Safe Room Building Permit Differs From Traditional Construction
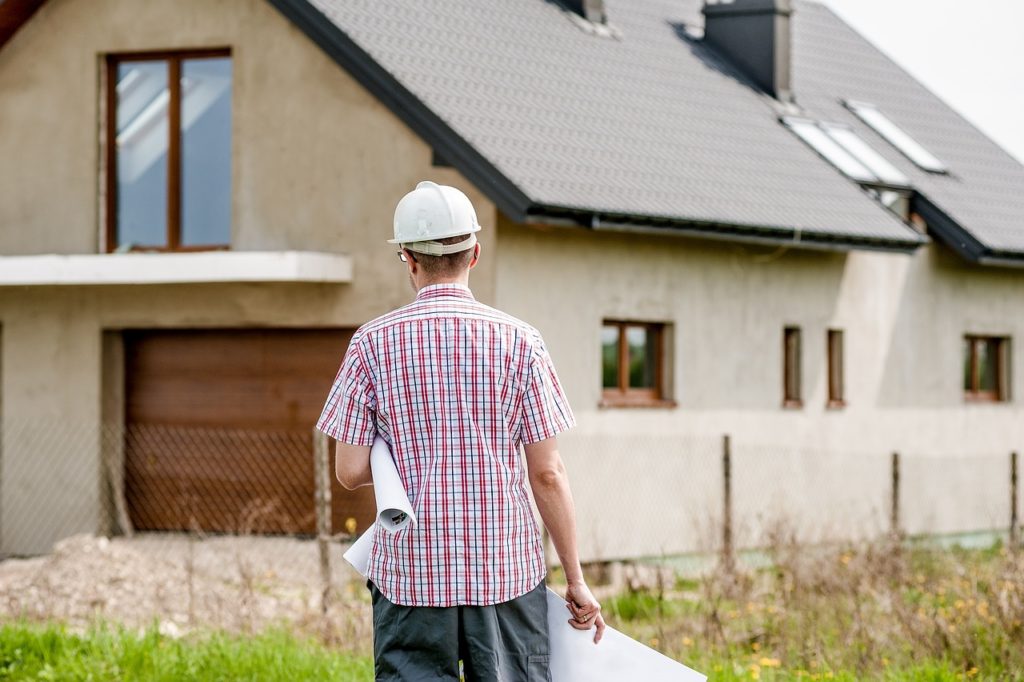
Unless you have previous construction equipment, understanding the nuances of the building permit process can be confusing and intimidating. Most building permits require a self-contractor questionnaire, lien agent form, proof of worker’s comp, scope of work, and blueprints. Because tornado shelter construction doesn’t differ that much than traditional home improvement projects, the same rules should generally apply. But here is where the safe room building permit process differs from most DIY projects. For starters, the light weight steel panels are easier to maneuver and fit in place than traditional building materials. And because a steel panelized kit can be easily you retrofitted room, there’s no disturbance to existing rooms, removing the burden of demolition. All you need are a few simple hand tools to complete your safe room in just one afternoon. Many towns and counties don’t even require a building permit for such minor construction. Either way, it’s best to pick up the phone and ask. Our knowledgeable building advisors can easily guide you through this process. We can even present a list of safe room alternatives, if we determine that an interior kit isn’t your best option.